Ultrasound Leak Detection for Power Generator Condensers
- CTRL Systems
- Nov 1, 2021
- 2 min read
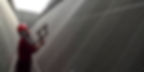
Ninety percent of the power plants in the United States are fueled by coal, nuclear materials, natural gas, and oil. These thermoelectric plants use the different types of fuel to boil water and create steam, which turns the turbines to generate the electricity. Once the steam has passed through the turbine, it must be cooled back into water for reuse by the condenser. The exhaust steam from the turbine is condensed back into water by transferring the heat to the condenser coolant, typically cold water. A common condenser is the surface condenser, also called a water-cooled shell and tube heat exchanger.
A secondary function of the condenser is to maximize turbine efficiency by maintaining a proper vacuum. Decreasing the operating pressure of the condenser (i.e. increasing the vacuum) therefore, increases the electric output of the turbine by increasing the enthalpy drop1 of the expanding steam. Operating the condenser at the highest vacuum increases plant efficiency allowing the plant to produce more electricity.
When a vacuum leak occurs in the condenser, non-condensable gases are introduced that must be vented. The gases increase the operating pressure, thereby reducing the turbine output and efficiency. The gases also decrease the heat transfer of the steam to the coolant and can cause corrosion in the generator.
Ultrasound Finds Leaks in Air-Cooled Condenser in Power Plant
A team of engineers was trained to use ultrasound for leak detection in a power plant with an air cooled condenser. A single day inspection found several vacuum leaks in the top of the tubes, inner tubes and tube junctions. The leaks were repaired; improving the vacuum system back pressure from 27 kPa to 9 kPA (power plant condenser design value is 13.7 kPa).
The increased vacuum pressure not only improved the operational efficiency of the condenser system, but also reduced coal consumption by 17,000 tons per year. The coal savings alone were $2.2 million USD. The power plant also saw an increase in electrical generation output.