Keeping Your Equipment and Employees Safe: Improving Safety By Using Airborne Ultrasound Inspection
- CTRL Systems
- Jul 15, 2021
- 2 min read
Updated: Aug 18, 2021
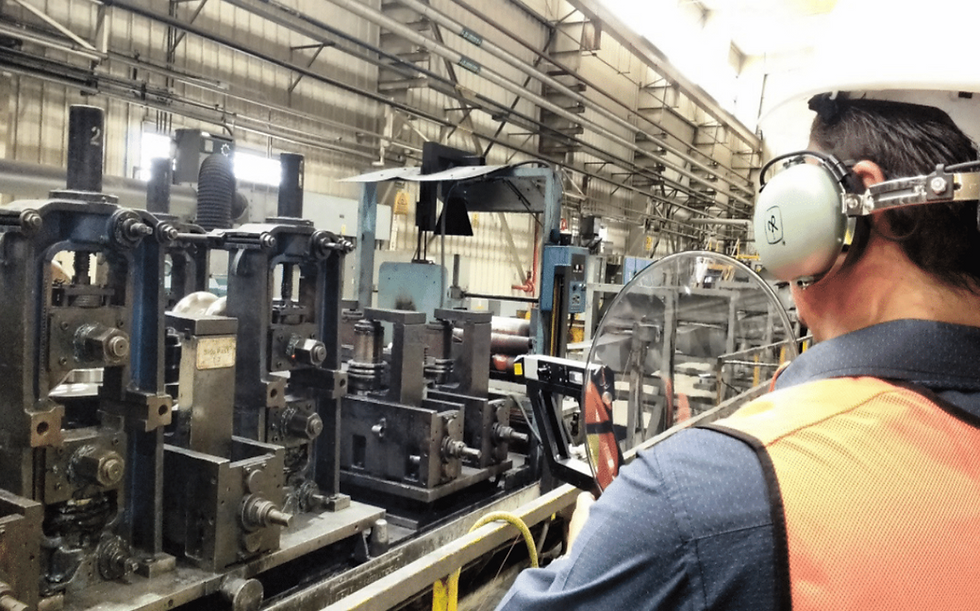
According to the Occupational Security of Health Administration, in 2015 around 2.9 million employees were injured or faced non-fatal illnesses at work, with over 50% of them resulting in disabilities requiring time off work. In the same calendar year, 4,836 fatalities were reported.
At CTRL Systems, our goal is not only to create products that can help monitor the health of your equipment but one that can also keep you and your employees safe as well. Ultrasound technology is excellent for detecting bearing health, but can also be modified to detect flammable gasses, toxic leaks, and even high voltage without having employees risk direct contact with energized parts and components.
The primary Ultrasound detector that we produce at CTRL Systems is the UL101, a handheld and lightweight detector designed to detect frequencies above 40kHz. By detecting these frequencies, the sound of turbulence (from pressurized gas), ionization of the atmosphere from electric deficient circuits, or friction from rotating elements can be detected. This can be useful when measuring the health of rotating elements like ball-bearings, which create these frequencies as they become more worn down.
When looking at gas leak detection, the traditional method was to use Personal Protection Equipment, often referred to as PPE. A PPE operates by detecting toxic or flammable gas in the air, as well as oxygen levels in the area. However, these devices cannot pinpoint the location of the leak. This not only creates a dangerous situation but requires a maintenance team to take time to look for the leak. Conversely, ultrasound detectors like the UL101 can be used directionally to detect turbulence generated by the leak itself as it accelerates from the escape orifice. Moreover, ultrasound devices can detect sound from all gas types, unlike PPE devices that are calibrated to specific gases.
Another area where ultrasound technology has helped to improve safety is in electric cabinets and transformers. The Electric Safety International Foundation found that between 2003 and 2015, there were 30,820 non-fatal electrical accidents, as well as 2,498 fatal accidents due to electrical incidents. Because these accidents have such a high fatality rate, industry effort has been placed on reducing their frequency. One way that CTRL Systems has approached the issue is to eliminate direct contact with the electrical components within electric cabinets and transformers. Because these cabinets are not hermetically sealed, ultrasonic frequencies can travel through the exterior of the panel, allowing them to be measured by the UL101. This eliminates the technician’s direct exposure to the energized components, greatly improving safety.
Safety has been improved with the inspection of rotating mechanical mechanisms with ultrasound technology as well. By using attachments like the PowerBeam 300 in conjunction with the UL101, an inspection can be conducted from up to 300 feet away, which also improves safety.
Overall, the most valuable asset to your business is your personnel. It is important to make sure that your physical assets are operating well, but it shouldn’t be at the expense of the employees’ safety. Ultrasound technology is an effective way to improve safety while ensuring the quality of information gathered about the operation of equipment.
Comments